Ausgestattet mit einem modifizierten 3D-Drucker erstellte der PC-Konstrukteur Jean Roberto De Lacovo alle Teile, die er für die Herstellung des Gehäuses für dieses atemberaubende Gerät benötigte 3D-gedrucktes PC-Gehäuse. Es heißt Piñasphere und verfügt über eine flüssigkeitsgekühlte 8-Kern-AMD Ryzen 7 APU.
Dank unseres rasanten Wachstums PC-Building-Facebook-Seite, wir haben viele maßgeschneiderte Gaming-PCs gesehen, von Mods, die auf vorhandenen Gehäusedesigns basieren, bis hin zu Scratch-Builds. Sie können Ihr Recht sogar zur Prüfung einreichen Hier. Lassen Sie uns zunächst herausfinden, wie Jean dieses atemberaubende 3D-gedruckte PC-Gehäuse hergestellt hat.
PCGamesN: Was hat Sie dazu inspiriert, diesen PC zu bauen?
Jean: Ich wollte sehen, wie weit ich mit dem Design eines Computergehäuses kommen kann. Wenn man über einen PC spricht, stellt man sich als Standard die kastenförmige Form vor – bis auf wenige Ausnahmen basieren die meisten Computergehäuse auf einer quadratischen Form.
An den Seiten sieht man diese schwarzen Wellenringe – ich wollte, dass sie wie die Wellen aussehen, die entstehen, wenn man etwas ins Wasser fallen lässt. Ich habe zu diesem Zeitpunkt bereits mit dem Tannenzapfen-/Ananas-Motiv für die Kuppel herumgespielt, daher dachte ich, dass diese Idee auch für die Wellenkämme sehr gut funktionieren würde, wenn auch mit vielen Optimierungen.
Auch die andere Hälfte der Kuppel wurde von der Natur inspiriert – sie basiert auf gefüllten Waben und jedes Sechseck ist aus der Nähe betrachtet komplex. Diese Komplexität hilft auch dabei, die Linien der Druckschicht weniger sichtbar zu machen. Der Innenraum hat eher einen Science-Fiction-Look mit vielen Polygonen. Es ähnelt strukturell einem Flugzeugrahmen – es ist keine Kugel, sondern eine komplexe Ikosphäre mit geometrischen Löchern, die ebenfalls den Luftstrom unterstützen.
Wie haben Sie diesen Bau geplant und gestaltet?
Normalerweise beginne ich meine Arbeit mit ein paar schnellen Bleistift- und Papierskizzen, aber diese hier begann mit einer Tinkercad-Skizze. Ich habe verschiedene Konfigurationen mit einigen 3D-Modellen getestet, die ich von den Hardwarekomponenten auf Tinkercad erstellt hatte. Dann dachte ich, wenn ich keine GPU installieren und ein externes Netzteil verwenden würde, könnte ich versuchen, eine Split-Sphere-Form zu erstellen.
Die erste Idee bestand darin, einen handgefertigten Metallrahmen aus 3 mm dickem Aluminiumblech zu verwenden. Allerdings habe ich kürzlich auch einige Experimente mit 3D-Druck durchgeführt, um ein Kamera-Rig herzustellen – während dieser Experimente habe ich die Festigkeit von PLA und PETG getestet und bin zu dem Schluss gekommen, dass PETG stark genug ist, um den Belastungen des Gehäuses standzuhalten.
Sie haben für den gesamten Bau den 3D-Druck verwendet – erzählen Sie uns alles über Ihren Prozess.
Anfangs war es schwierig, aber jetzt würde es viel schneller gehen. Ich musste anfangen, es anders zu planen als bei einem gewöhnlichen Case-Mod, weil ich kein Material entfernte, sondern es hinzufügte. Ich habe einige Tests mit verschiedenen kleinen Projekten durchgeführt, um die Einstellungen des 3D-Druckers zu optimieren.
Die Software, die ich als Slicer für die Ausdrucke verwendet habe, war Ultimaker Cura 4.13. Ich fand sie von Anfang an intuitiv und ermöglichte mir die Feinabstimmung meiner Ausdrucke. Ich habe zum Beispiel gelernt, die Z-Nahtausrichtung so einzustellen, dass auf den Drucken keine sichtbare Linie entsteht, und die Rückzugseinstellungen für verschiedene Situationen festzulegen – Sie können die Einstellungen grundsätzlich an Ihre Bedürfnisse anpassen.
Mein Arbeitspferd 3D-Drucker ist ein Creality Ender 3 Pro, den ich modifiziert habe, da er mir zu laut war. Ich habe ein Creality Silent Mainboard sowie einen 120-mm-Lüfter für das Netzteil hinzugefügt und außerdem die benutzerdefinierten Lüfterkanäle für den Drucker mit PETG entworfen und gedruckt, wodurch ich anstelle der standardmäßigen 40-mm-Lüfter ein duales 60-mm-Noctua-Lüfter-Setup verwenden kann .
Es verfügt jetzt auch über einen direkten Extruder – ich musste den Rückzug viel stärker reduzieren als erwartet, da die ersten Drucke mit dem neuen Setup beim Drucken mit PETG zu Verstopfungsproblemen des Extruders führten.
Insgesamt besteht Piñasphere aus 27 3D-gedruckten Teilen. Für den letzten Schliff habe ich Präzisionsschneider und ein Feuerzeug verwendet, um überschüssiges Material oder Fäden zu entfernen. Nachdem ich jedoch die richtigen Filamenttemperaturen eingestellt hatte, stellte ich fest, dass die Besaitung äußerst begrenzt war.
Ich habe auch festgestellt, dass die Ausrichtung der Teile während des Druckvorgangs bei der Endbearbeitung hilfreich war. Ich wähle bewusst die Basis als Kontaktseite zwischen den Teilen, da man mit dieser Seite weniger Kontrolle über das Finish hat, wenn man es anschließend nicht lackiert.
Ein wichtiger Punkt, den ich gelernt habe, ist, dass es Zeit und Geduld erfordert, die Teile mit Präzisionsschneidern perfekt zu reinigen – machen Sie einen Fehler und werfen Sie am Ende das gedruckte Teil weg – das passierte mit einem SSD-Rahmen, den ich gedruckt habe. Das Reinigen und Nivellieren des Druckers nimmt ebenfalls etwas Zeit in Anspruch, löst aber die meisten Probleme, die während des Druckvorgangs auftreten können – das Drucken mit einer langsameren Geschwindigkeit hilft auch, viele Probleme zu vermeiden.
Wie passen alle Teile zusammen?
Es handelt sich im Grunde um eine Super-Sandwich-Struktur – wie bei Flugzeugen werden einige Teile einfach zwischen die befestigten Schichten gepresst. Die Teile sind so geformt, dass sie nur richtig zusammengebaut werden können – auch wenn es nur eine andere Ecke oder ein anderes Loch ist, jedes Teil hat immer einen Aspekt, der bei der Positionierung hilft. Diese Struktur ermöglichte es mir, ein Chassis mit ausreichender Festigkeit, aber minimaler Füllung zu schaffen, wodurch das Gewicht und die Menge des verwendeten Materials minimiert wurden.
Zur Befestigung habe ich dann Edelstahlschrauben verwendet – das Motherboard wird mit M3-Schrauben mit 10-mm-Gewindeeinsätzen aus Messing befestigt – man kann sie mit einem Lötkolben erwärmen und dann in die 3D-gedruckten Teile drücken. Für die restlichen Befestigungen habe ich das PETG mit Werkzeug eingeschraubt und Halbrundkopfschrauben M5 verwendet – die Gewindeabschnitte sind mindestens 10 mm lang.
Die weißen Dome rasten derweil einfach auf der Mainboard-Seite ein und befestigen sie mit einer leichten Drehung im Uhrzeigersinn auf der Kühlerseite – hier ist kein Werkzeug nötig.
Was für ein kleines Motherboard ist das?
Ich habe ein ASRock X300M-STX-Motherboard verwendet. Es war eines der kleinsten Motherboards, die ich finden konnte, und ermöglichte mir die Verwendung eines AMD Ryzen 7 5700G. Es unterstützt bis zu 64 GB Arbeitsspeicher und verfügt über zwei M.2-SSD-Steckplätze und zwei SATA-Anschlüsse für 2,5-Zoll-SSDs, sodass ich ausreichend Platz zum Aufrüsten von Arbeitsspeicher und Speicher habe, was dazu beitragen wird, dass dieses Gerät auch in Zukunft nützlich bleibt. vielleicht als Büro-PC oder Server.
Welche Herausforderungen stellte die Form des Gebäudes dar?
Ehrlich gesagt, wenn man hauptsächlich an die Form und nicht an die Abmessungen denkt, ist es relativ einfach, einen PC mit einer ungewöhnlichen Form zu bauen – die größte Herausforderung für mich bestand darin, im Gehäuse genügend Platz zu lassen, damit die gesamte Ausrüstung gut funktionieren kann.
Eine weitere große Herausforderung stellten die beiden I/O-Panels dar – ich hatte beschlossen, dass beide wie das Frontpanel aussehen und in einer Aussparung der Kuppel platziert werden sollten, aber ich musste auch etwas Platz für das Netzkabel lassen , und deshalb ist das „Stück“ auf dieser Seite so lang.
Welches Netzteil hast du verwendet?
Es handelt sich um das externe Netzteil, das im Lieferumfang des ASRock Deskmini X300 enthalten ist. Es sieht aus wie ein Laptop-Netzteil und hat eine Leistung von 120 W bei 19 V – es ist eher klein und daher perfekt für diesen PC geeignet, da es kein stromhungriges Monster ist.
Wie haben Sie die Kabelführung geplant?
Alle Kabel werden im mittleren Ring verlegt, der auch den Hauptrahmen bildet – er verfügt über viele Leerräume für die Luftzirkulation und die Kabelführung. Die Kabel für den Netzschalter, die SSD-Aktivitäts-LED und die Power-LED werden unter der Hauptplatine verstaut und gelangen dann in die Box, die als Haken für die Domes dient und auch den Netzschalter enthält.
Das Kühlerlüfterkabel wird durch den Kuppelhaken unter dem Kühler verdeckt – ich habe einen Kabelkanal dafür erstellt – dann verläuft es durch den Durchgang für eines der Kühlrohre und bleibt unter dem Kühlrohr auf der Motherboard-Seite verborgen. Die WLAN-Antennenkabel sind unter der Hauptplatine versteckt und ihre Anschlüsse an der Oberseite der Hauptplatine sind unter der M.2-SSD verborgen, sodass Sie sie einfach nicht sehen können. Zuletzt wurden die Kabel des Wasserblocks unter den Befestigungsflügeln des Wasserblocks verlegt.
Erzählen Sie uns, wie das Luftstromsystem funktioniert.
Das ist einer der Teile, die mir in meinen Projekten am besten gefallen. Nachdem sie den Kühler passiert hat, strömt die Luft durch den mittleren Kanal, kühlt die 2,5-Zoll-SSD, bewegt sich dann unter das Motherboard und tritt aus einem 5-mm-Spalt zwischen dem Motherboard und seinem Stützrahmen aus – sie strömt fast um den gesamten Umfang herum.
Zu diesem Zeitpunkt ist die Luft jedoch noch nicht draußen – die interne Kuppel leitet sie dann, um sich um das Motherboard zu bewegen, sodass sie die M.2-Module und den VRM-Kühlkörper des Motherboards kühlt. An der Seite des Kühlers befinden sich außerdem zwei Löcher, die den Gegendruck, der durch die Luftbewegung im mittleren Kanal entsteht, etwas entlasten.
Wie haben Sie die kupferfarbenen Akzente erzielt?
Ich wollte eine warme Farbe als Kontrast zum Weiß hinzufügen und hatte ursprünglich überlegt, Ringe aus echtem Kupfer zu verwenden. Während der Skizzierphase wollte ich jedoch mehr reflektierende Facetten hinzufügen, als es bei Ringen der Fall ist, also habe ich sie mit einer komplexeren Form gedruckt.
Wenn ich viel Zeit gehabt hätte, hätte ich sie von Hand herstellen können, aber dieses Mal wollte ich es selbst testen und sehen, was ich allein mit dem 3D-Druck machen könnte, also habe ich Giantarm Silk Copper Filament gekauft und die Ergebnisse haben mich nicht enttäuscht – Sie verleihen dem Bau eine Premium-Atmosphäre.
Welche Spezifikation haben Sie gewählt und warum?
Ich wollte, dass es von allem etwas kann, aber die 3D-Bearbeitung war ein Muss. Ich wollte auch, dass das Gerät bei 1080p-Gaming eine ordentliche Leistung erbringt. Da es keinen Platz für eine Grafikkarte gab, fiel die Wahl offensichtlich auf die beste APU, die ich kaufen konnte, und das war der AMD Ryzen 7 5700G – ich liebe ihn; Es ist ein ausgezeichneter Darsteller.
Der Build verfügt über 16 GB Speicher, da ich im Oktober und November nach der Hardware gesucht habe und sie damals im Angebot war. Corsair ist eine gute Marke, also habe ich meine Chance genutzt und sie gekauft.
Ich werde den RAM in den nächsten Monaten aufrüsten, da Sie mit dem ASRock-Motherboard den gemeinsam genutzten Video-RAM auf bis zu 16 GB erhöhen können, wenn Sie über mehr als 32 GB Systemspeicher verfügen.
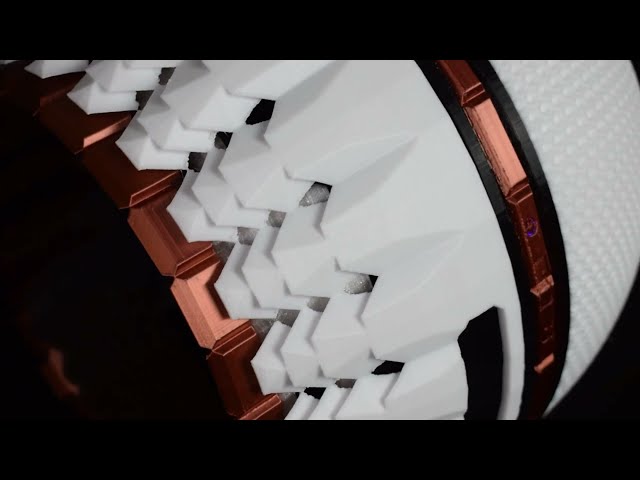
Sind Sie auf Schwierigkeiten gestoßen?
Ich denke, die größte Herausforderung bestand darin, das Druckerprofil für jedes Filament genau abzustimmen. Ich musste die Druckfehler reduzieren, die sich nicht verbergen ließen, da eines meiner Ziele darin bestand, den Aufbau gut aussehen zu lassen, ohne ihn lackieren zu müssen.
Ich habe mich daran gewöhnt, den Extruder gründlich zu reinigen, und habe mir außerdem eine lange Edelstahlnadel gekauft, um alle Filamentreste daraus zu entfernen.
Wie lange haben Sie von Anfang bis Ende für die Fertigstellung dieses Builds gebraucht?
Nach der Phase des Kennenlernens der 3D-Bearbeitung würde ich sagen, 3-4 Monate. Es würde definitiv weniger Zeit in Anspruch nehmen, wenn ich es jetzt tun würde.
Sind Sie mit dem Endergebnis rundum zufrieden oder wünschen Sie sich im Nachhinein, dass Sie einiges anders gemacht hätten?
Ich bin absolut zufrieden – das war das erste Mal, dass ich versucht habe, ein 3D-gedrucktes Gehäuse zu bauen, und vor der Endmontage war ich mir nicht hundertprozentig sicher, wie es aussehen würde. Nachdem ich alles zusammengebaut hatte, hatte ich jedoch nur einen Gedanken: „Wow, es ist solide und sieht wirklich cool aus!“ Ich könnte wirklich nicht glücklicher sein.
Pinasphere 3D-gedruckte PC-Spezifikationen
- CPU: AMD Ryzen 7 5700G
- GPU: Integrierte AMD Radeon RX Vega11
- Lagerung: 1 TB Samsung 980 M.2 SSD, 250 GB Samsung 860 Evo 2,5 Zoll SATA SSD
- Erinnerung: 16 GB (2 x 8 GB) Corsair Vengeance 3200 MHz DDR4 SODIMMs
- Hauptplatine: ASRock X300 M-STX
- Netzteil: Externes 120-W-ASRock-Netzteil
- Kühlung: Cooler Master MasterLiquid ML120L V2 AIO Flüssigkeitskühler
Erstaunliche Arbeit, Jean. Dies ist ein wirklich einzigartiger kundenspezifischer PC – das Design ist hervorragend und Sie haben auch gezeigt, dass Sie wirklich ein verdammt gut aussehendes 3D-gedrucktes PC-Gehäuse herstellen können sowie.
Dieser Beitrag erschien ursprünglich auf Custom PC, das seit über 20 Jahren erstaunliche Setups behandelt und jetzt Teil von PCGamesN ist. Tritt unser … bei Facebook-Gruppe mit 500.000 Mitgliedern um diesen Build zu besprechen.
ICHWenn Sie sich für einen erfahrenen PC-Hersteller halten, ist das möglich Reichen Sie uns noch heute Ihren individuellen PC-Build ein um die Chance zu haben, in Zukunft auf PCGamesN vorgestellt zu werden.